Визуально-измерительный контроль
Определяет поверхностные дефекты, дефекты формы шва и геометрию согласно требованиям НТД. Визуально-измерительный контроль проводится с использованием измерительных средств таких как: универсальные шаблоны сварщика, рулетка, штангенциркуль и т. д. С помощью визуально-измерительного контроля обнаруживают: коррозионные поражения, трещины, изъяны материала и обработки поверхности и пр. Осмотр проводят с использованием оптических приборов, расширяющих пределы естественных возможностей глаза.
100%
Внешние дефекты
Внутренние дефекты
Сложность проведения контроля
Время проведения
Требования к подготовке поверхности
Ржавчины
ЛКП
Масла
- РД 03-606-03
Визуально-измерительный контроль (ВИК) является одним из методов неразрушающего контроля (НК), который предваряет все остальные методы. Он регламентируется инструкцией РД 03-606-03 по визуальному и измерительному контролю, утверждённой постановлением № 92 Госгортехнадзора России от 11.06.2003 г. ВИК проводится с целью выявления поверхностных дефектов на объектах контроля (ОК), которые возможно обнаружить либо невооружённым глазом, либо с использованием зеркал, луп, эндоскопов, микроскопов и других оптических приборов.
При монтаже различных механизмов, строительстве сооружений и прокладке коммуникаций, а также их ремонтах и реконструкциях применяется, как правило, оптика с 2 – 7-кратным увеличением. В процессе эксплуатации таких объектов контроль за их исправностью и техническим состоянием производится с применением оптических приборов до 20-кратного увеличения.
Визуально-оптический контроль позволяет выявлять в местах, доступных для наблюдения, а также в скрытых полостях различного технологического оборудования такие дефекты, как:
- трещины, поры, раковины;
- заусеницы;
- расслоения;
- прожоги;
- наплывы и другие дефекты.
Одновременно с визуальным контролем, либо непосредственно после него, ведётся контроль измерительный, при котором определяются конкретные физические величины обнаруженных дефектов с помощью простейших технических средств. Также проводятся измерения геометрических параметров сборочных элементов и узлов на предмет их соответствия нормативным документам.
Для проведения такого контроля применяются контрольные и измерительные средства с метрологическими характеристиками, определяющими:
- пределы измерений и их диапазон;
- цену деления шкалы прибора;
- допустимую величину погрешности.
Такие приборы, инструменты и средства комплектуются в наборы соответствующие ОК, будь то сварное соединение, резервуар, строительная конструкция и др. Все средства измерений, входящие в комплекты, должны пройти аттестацию по ГОСТ Р 8.568, государственную поверку по ПР 50.2.006-94 и быть откалиброванными по ПР 50.2.016-94.
ВИК производится:
- при входном контроле заготовок, материала и деталей для проверки их геометрических размеров и обнаружения возможных дефектов;
- при подготовке сборочных единиц, заготовок и деталей к сборке и сварке;
- в процессе сварки, либо по её окончании — для обнаружения возможных дефектов в сварном соединении;
- после устранения обнаруженных дефектов в сварном соединении и основном материале;
- периодически, в течение всего срока эксплуатации строительных конструкций и технических устройств.
ВИК является самым простым и практичным методом НК, не требующим специального дорогостоящего оборудования и инструментов. При этом он позволяет обнаруживать большое количество различных поверхностных дефектов, — на его долю приходится почти половина всей полученной при НК информации.
При всей своей простоте, проведение такого контроля должно поручаться специально обученному, в соответствии с ПБ-03-440-02, и дипломированному специалисту, который обязан оформлять результаты проведённого контроля соответствующим документом.
Как и всякий метод НК, ВИК имеет свои плюсы и минусы. К преимуществам относятся:
- простота и доступность метода;
- сравнительно высокая скорость проведения контроля;
- высокая информативность;
- дешевизна приборов и оборудования;
- возможность неоднократной перепроверки результатов для их подтверждения или уточнения.
Основной недостаток — человеческий фактор, влияющий на получаемые результаты; кроме того:
- возможен контроль только видимой части ОК;
- невозможность выявления дефектов размером менее 0,1 мм.
Неразрушающий контроль трубопроводов тепловых сетей
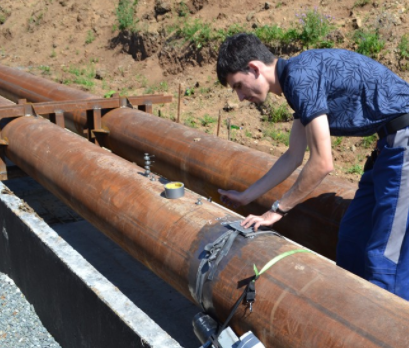