Капиллярный контроль
Капиллярный контроль проникающими веществами обнаруживает несплошности, выходящие на поверхность объекта контроля. Капиллярный метод основан на проникновении индикаторной жидкости — пенетранта в полость дефекта. Оставаясь в несплошности после обработки поверхности, пенетранты образуют над дефектом индикаторный рисунок, который регистрируется визуально.
1мкм
Внешние дефекты
Внутренние дефекты
Сложность проведения контроля
Время проведения
Требования к подготовке поверхности
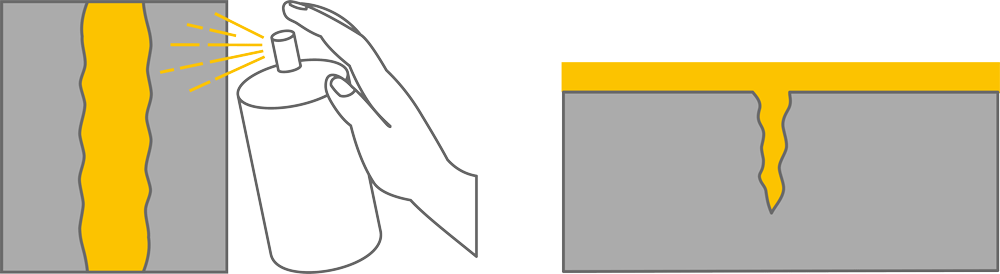
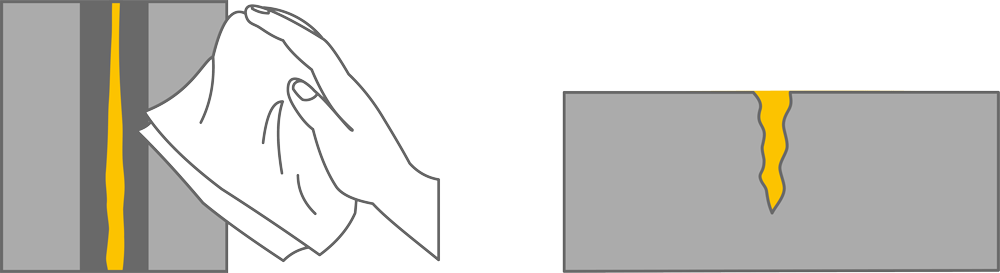
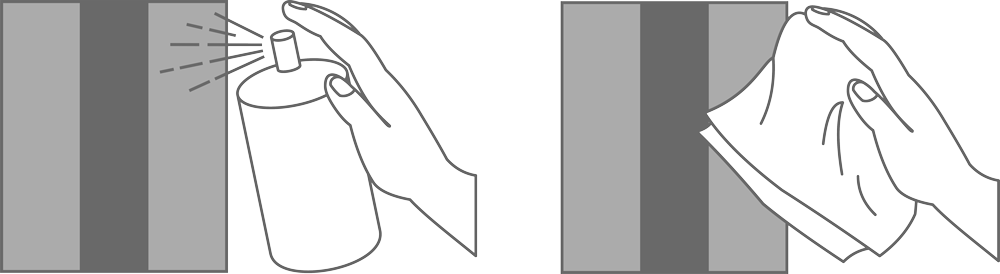
Капиллярный неразрушающий контроль проводят для того, чтобы оценить состояние поверхности объекта на предмет наличия пор и трещин, раковин, непроваров. Словом, тех дефектов, которые представляют собой выходящие на поверхность микроскопические полости. Например, если трещину невозможно определить визуальным методом, то капиллярный контроль с этим справится.
Капиллярная дефектоскопия широко распространена из-за низких затрат на производство контроля, которые обусловлены относительно малой стоимостью расходных материалов и «нехитрой» технологией. Метод основывается на способности жидких индикаторных составов под действием капиллярного эффекта проникать в полости дефекта.
Суть метода заключается в специальной обработке поверхности объекта контроля. Она тщательно очищается, затем на неё наносится индикаторное вещество — пенетрант. Иногда, ещё и проявитель. Это зависит от технологии, цветная она или флуоресцентная. Затем дефекты наблюдают визуально по цветному рисунку, либо в ультрафиолетовом свете, когда используются люминесцентные пенетранты.
Капиллярными методами проверяют металлические детали, изделия из керамики, стекла, пластмасс и других материалов. Можно исследовать объекты любых размеров и геометрии. К деталям из ферримагнитных металлических сплавов также возможно применение капиллярной дефектоскопии, если по условиям их эксплуатации магнитопорошковый контроль неприменим. Исследования пенетрантами регламентируются указаниями и нормами, изложенными в ГОСТ 18442.
Контроль проникающими веществами во многих случаях предписывают проводить как перед сдачей готовых объектов в эксплуатацию, так и в процессе само́й эксплуатации. То же самое касается и отдельных деталей, например, лопаток паровых турбин или судовых винтов. Применяется такой контроль:
- в строительстве;
- в энергетике;
- в судостроении и автомобилестроении;
- в химической и металлургической промышленности;
- в авиационной и ракетной технике.
Существует несколько методов капиллярного контроля. В отношении условий его проведения, применяемых расходных материалов, а также способам регистрации дефектов, методы контроля проникающими веществами подразделяют на хроматические, ахроматические и люминесцентные.
Процесс выявления дефектов включает в себя пять обязательных процедур:
- тщательная очистка поверхности изделия;
- нанесение проникающего пенетранта путём аэрозольного распыления или полива;
- удаление излишков пенетранта с поверхности;
- обработка поверхности проявителем, если речь идёт о цветной дефектоскопии;
- расшифровка индикаторного рисунка визуально при естественном освещении или с использованием ультрафиолетовых источников света, если речь идёт о люминесцентной дефектоскопии.
Очистка объекта заключается в удалении всех загрязняющих веществ, а также защитного покрытия с проверяемой поверхности путём химической обработки, механическим и иным способом. Далее производится сушка объекта. При выполнении этой процедуры следует руководствоваться методическими указаниями РД 153 -34.1-17.461-00.
Нанесение пенетранта возможно несколькими способами. Объект может погружаться в ванну с пенетрантом или поливаться им. Как правило, данные способы применяются в автоматизированных линиях на участках производственного контроля. Пентрант также может наноситься кистью. Но наибольшее распространение получил способ аэрозольного напыления. Он применим для большей части объектов, и не требует наличия специального оборудования.
Удаление лишнего пенетранта производится либо салфеткой без ворсинок, либо путём отмывания поверхности водой или очистителями, предназначенными для предварительной очистки объекта. В дальнейшем поверхность необходимо просушить и протереть чистой гигроскопичной тканью.
Нанесение проявителя лучше производить одним или двумя-тремя тонкими слоями, чтобы его избыток не затемнял индикаторный рисунок. Пенетрант, находящийся в полостях дефектов, диффундирует в проявитель и, благодаря адсорбции, проявляется на поверхности в виде контрастного индикаторного следа, ширина которого многократно превосходит ширину трещины.
Расшифровка индикаторного рисунка производится визуально или с применением оптики. При использовании люминесцентных пенетрантов необходимо применять ультрафиолетовые светильники и защитные очки. Результаты контроля могут быть зафиксированы видео-фотоаппаратурой, либо клейкой плёнкой.
Методы капиллярного контроля имеют целый ряд неоспоримых достоинств, среди которых:
- универсальность;
- доступность метода и его простота;
- отсутствие сложной аппаратуры;
- портативность метода и мобильность;
- низкая себестоимость проведения контроля;
- возможность выявления сквозных дефектов в тонкостенных деталях;
- обнаружение микроскопических несплошностей сечением = 0.1-50 мкм.
К недостаткам следует отнести невозможность обнаружения внутренних дефектов, не выходящих на поверхность. Существенным недостатком является критичность к уровню шероховатости поверхности объекта; допустимая шероховатость = Ra 3,2 (Rz 20).
Неразрушающий контроль трубопроводов тепловых сетей
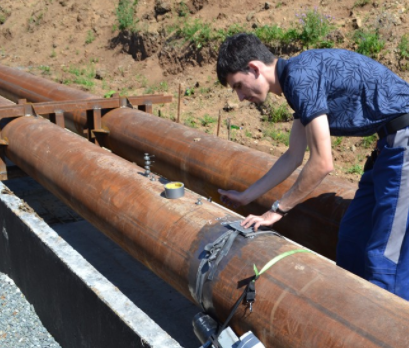